Mitä ovat polyeteenipelletit ja missä niitä käytetään?

Artikkelissamme kerromme sinulle rakeisen polyeteenin ominaisuuksista ja sen käytön laajuudesta. Tarkastellaanpa tarkemmin sen tuotanto- ja kierrätysmenetelmiä.
Erikoisuudet
Granulointi on eteenipolymeerien valmistuksen minkä tahansa teknisen vaiheen viimeinen vaihe. Suurin osa kaikesta polyeteenistä valmistetaan rakeiden muodossa, toisin sanoen tietyn kokoisina kiinteinä hiukkasina.
Rakeistustekniikka auttaa ratkaisemaan kolme ongelmaa kerralla:
- polymeerien viimeistely - lisäainejäämien ja kemiallisten liuottimien poisto, materiaalin mekaanisten ominaisuuksien parantaminen, kaasunpoisto sekä homogenointi;
- antaa tuotteen suorituskykyominaisuudet, tarvitaan polyeteenin järkevämpään käyttöön muovituotteiden luomisessa;
- materiaalien luominen kaikenlaisilla lisäaineilla muuttaa polyeteenin kemiallisen stabiilisuuden, tiheyden, optisten ja dielektristen ominaisuuksien parametreja.

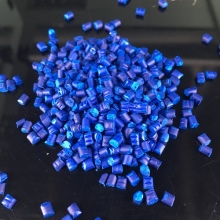

Rakeiden muodossa olevalla polyeteenillä on merkittäviä etuja verrattuna hiutaleeseen ja jauheeseen.
- Tilavuuden vähennys puoleen (bulkkipolyeteenin tiheys jauhe- ja rakeisessa muodossa on 0,20-0,25 g / cc ja 0,5-0,6 g / cc). Näin voit vähentää merkittävästi tuotteen varastointi-, siirto- ja pakkauskustannuksia.
- Korkea juoksevuus - rakeiden käyttö ei aiheuta ongelmia pakkaamisen eikä kuljetuksen aikana. Muovirakeet eivät tartu laitteiden seiniin, eivät keräänny kuljetusmekanismien solmuihin, eivät sähköisty eivätkä muodosta "kuolleita vyöhykkeitä", jotka aiheuttavat tuotantoprosessien epävakautta ja teknisten laitteiden sammumista.
- Esityksen menetyksen minimoiminen - polyeteenirakeet kaadetaan kokonaan ulos säiliöistä ja lastausmekanismeista.
- Alhainen alttius valovanhenemiselle ja tuhoutumiselle... Pölyn muodostumisen vähentäminen tuotannon aikana nollaan ja sen seurauksena työolojen parantaminen.



Kuivauksen ja kaikkien tuotteiden laatuvaatimusten noudattamista koskevien testien jälkeen rakeinen polyeteeni pakataan 25 kg:n pusseihin ja merkitään. GOST-standardien mukaan erän rakeilla on oltava sama geometria ja koko kaikkiin suuntiin alueella 2–5 mm, ja niiden on oltava samanvärisiä. Jokainen erä voi sisältää rakeita, joiden tilavuus on 5–8 mm ja 1–2 mm, mutta enintään 0,25 % ja 0,5 %. Elementit, joissa on selvät viat (vieraat sulkeumat ja polymeerin hajoamisesta johtuva karhea pinta), hylätään.
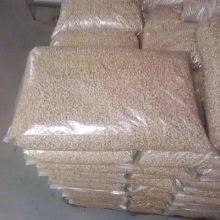


Käyttöalueet
Rakeisen polyeteenin käyttöalue kattaa yli 80 % kaikista polyeteenin käyttöalueista yleensä. Listataan yleisimmät alueet.
- Erimuotoisten ja -kokoisten kalvojen valmistus... Tätä varten rakeet ladataan erityiseen suppiloon, kuumennetaan ja sekoitetaan. Kaikkien manipulointien tuloksena saadaan sula massa. Siitä valmistetaan ekstruusiolla tietyn paksuinen kalvo. Pyöreäpäinen ekstruuderi on teollisuudessa laajalti kysytty. Tällä menetelmällä voit saada hihan, jota voidaan käyttää pussin jatkovalmistukseen.
- Konttituotanto. Pakkausmateriaalit, kuten ruukut, laatikot, pullot ja vastaavat tuotteet, valmistetaan ruiskupuristamalla ja muilla muovaustekniikoilla. Tässä tapauksessa rakeinen polyeteeni muodostetaan tyhjiössä - tätä menetelmää pidetään taloudellisesti kannattavimpana ja käytännöllisimpana.
- Sähköeristyksen luominen erikoiskaapelimerkkien polyeteenistä. Tämä menetelmä on samanlainen kuin ensimmäinen: rakeet sulatetaan ja sekoitetaan homogeeniseksi. Tarvittavan muotoinen eristemateriaali valmistetaan sitten ekstruusioprosessilla.
- Vaahdotetun polyeteenin valmistus (polyeteenivaahto). Se on yksi suosituimmista lämmöneristysmateriaaleista. Sen vapauttamiseen käytetään myös rakeisten polymeerien sulatetta.
- Ajoneuvojen korielementtien ja muiden korkeaa lujuutta vaativien tuotteiden valmistus... Tätä varten ruiskuvalulla muovataan erikoislaatuisia polyeteenirakeita.



Granulaattorit ja muut laitteet
Rakeisen polyeteenin tuotanto sisältää useita vaiheita.
Aluksi raaka-aine valmistellaan, eli jauhataan. Sen mukaan, mihin luokkaan käsitelty materiaali kuuluu, silppureita on useita tyyppejä:
- näytteitä polymeerikalvoille - optimaalinen polypropeenin, akryylin sekä nailonin, PVC:n ja muiden vastaavien tuotteiden jäämille kalvomuodossa;
- myllyt - soveltuu ohuiden muovituotteiden, kuten PET-pullojen, käsittelyyn;
- murskaimet - ovat välttämättömiä massiivisten tuotteiden, kuten PVC-parvekkeen ja muiden yleisrakenteiden murskaamiseen.
Valmistetut raaka-aineet pestään, tätä varten he käyttävät "märkämurskaimia",
Toiminnallisesti ne voivat yhdistää raaka-aineiden jauhamisen pesuun.


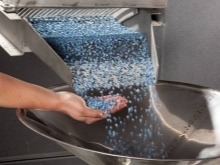
Ylimääräinen kosteus poistetaan kuivausyksiköillä, yleensä niitä käytetään:
- sentrifugit;
- kuivaus lämmitetyllä ilmalla;
- kuivaus paineilmalla;
- spin-puristimet;
- ruuvityyppiset vedenerottimet.
Silputut, puhdistetut ja kuivatut muovit voivat sisältää polymeerijäämiä, koska Käsin tapahtuva alkulajittelu ei tarjoa 100-prosenttista erottelua... Kaikkien tarpeettomien elementtien poistamiseksi muovin käsittelyyn tarkoitettujen tuotantolinjojen rakenteeseen tuodaan erikoistuneet erotusmekanismit.

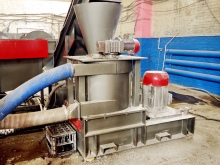

Kuvataan yleisimmät muovilastujen erottamistekniikat.
- Flotaatioerottelu... Menetelmä perustuu erotettavien materiaalien kostutusparametrien eroon. Erottamisen suorittamiseksi valmistettu seos syötetään säiliöön, jossa on hapella rikastettua vettä. Hydrofobisen materiaalin hiukkaset peittyvät välittömästi ilmakuplilla ja kelluvat. Hydrofiiliset materiaalit kerääntyvät säiliön pohjalle.
- Sähköstaattinen erotus. Tämä menetelmä perustuu eroon sähkönjohtavuudessa ja materiaalien herkkyydessä pinnan staattisen sähköistyksen kertymiselle. Käsittelyn aikana materiaalin hiukkaset sekoittuvat voimakkaasti, kitkan seurauksena niiden pinta sähköistyy voimakkaasti ja saa siten tietyn suuruisen sähkövarauksen. Erottamisen avulla voit erottaa materiaalit, joilla on erilaiset ominaisuudet sähkökentässä.
- Fotometrinen erotus... Tämän mekanismin toiminta perustuu muovin erottamiseen optisten ominaisuuksien eli heijastavuuden ja värin mukaan.
Tämän tyyppiset asennukset on varustettu erityisillä sähkömagneettisten signaalien lähettimillä sekä erittäin herkillä antureilla.



Viimeinen vaihe missä tahansa rakeisen muovin valmistusprosessissa on suora rakeistus, jota varten käytetään polyeteenirakeistuslaitetta. Tämän laitteen avulla voit ratkaista useita ongelmia kerralla:
- esitellä valmiita tuotteita;
- komposiittimateriaalien saamiseksi erilaisilla lisäaineilla.
Polyeteenigranulaattori toimii samalla tavalla kuin ekstruuderi.Siinä olevat muoviaihiot sekoitetaan erityisillä liikkuvilla ruuveilla, ja ne kulkevat myös vyöhykkeiden läpi, jotka eroavat lämmityslämpötilasta. Sen kohonneiden arvojen ja sekoituksen aikana syntyvän kitkan vaikutuksesta massa alkaa sulaa ja ulostulona on kuituja, joilla on annetut poikkileikkausparametrit. Jotta ne eivät tarttuisi toisiinsa, ne kastellaan vedellä. Kun ne on leikattu erityisellä laitteella, kiinnittyen tiettyyn pituuteen. Juuri näitä segmenttejä kutsutaan rakeiksi. Jäähdytystä varten kuumennetut rakeet laitetaan vedellä täytettyyn rengasputkeen, josta ne siirtyvät sentrifugiin, jossa massa vapautuu nestekomponentista. Sitten raaka-aine tulee kuivauskammioon, ja loppuvaiheessa kuivattu materiaali kuljetetaan täyttöyksikköön.
Polyeteenirakeistimen avulla voit muuttaa tilaa vievän polymeerin vahvaksi ja tiheäksi materiaaliksi. Lähtörakeilla on yhtenäinen muoto ja koko, yhtenäinen rakenne.
Jokaisessa rakeistusvaiheessa saadun materiaalin laadun valvonta on pakollista.

Kierrätysprosessi
Viime vuosina muovin kierrätykseen osallistuvien valmistusyritysten määrä on lisääntynyt huomattavasti. Ja tässä ei ole kyse vain ympäristöongelmista, vaan myös tällaisen liiketoiminnan näkymistä. Polyeteenistä tulee ihanteellinen pohja roskasäiliöiden, kaikenlaisten kotitaloussäiliöiden, muovipaneelien ja muiden esineiden luomiseen.
Kalvojen ja pussien kierrätys ei käytännössä aiheuta erityisiä vaikeuksia, koska niiden rakenne ei muutu. Mutta tätä ei voida sanoa saadun tuotteen laadusta - jokaisella käsittelyjaksolla läpinäkyvyysparametrit ja granulaatin väri huononevat merkittävästi.
Vastaavasti myös jatkokäytön laajuus pienenee.
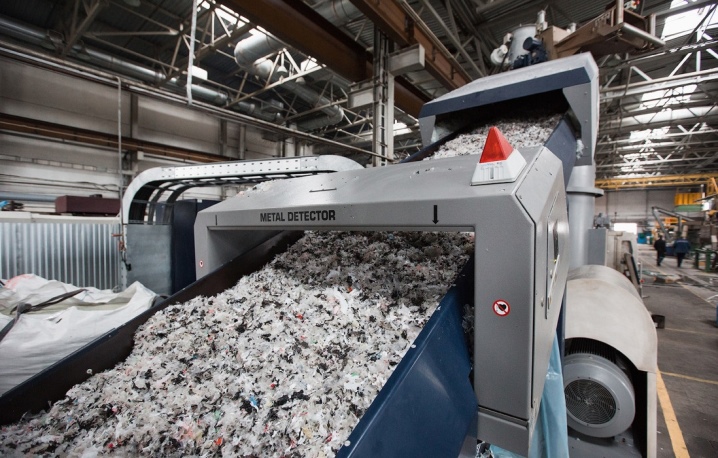
Voit oppia muovirakeiden käsittelystä kotona alla olevasta videosta.
Kommentti lähetettiin onnistuneesti.